Optimising warehouse layout is critical for any manufacturing company looking to streamline operations, improve productivity, and reduce costs. With a well-planned warehouse, your team can efficiently locate, store, and dispatch items, directly impacting production. It’s important to regularly review and update your warehouse layout to ensure it remains as efficient and safe as possible, allowing your business to thrive in a competitive market.
By implementing these practical steps, your warehouse will become an investment that not only supports but actively drives business growth and ensures that your business and staff are working to their full potential.
The importance of warehouse layout
- Reduced operating costs: Minimises the time and distance required to move items, cutting down on labour and transport
- Enhanced productivity: An efficient layout enables faster picking, packing, and shipping, reducing errors and improving fulfilment times
- Improved safety: A structured, logical design reduces the risk of accidents and injuries.
- Scalability: An optimised layout allows for flexibility and can accommodate business growth
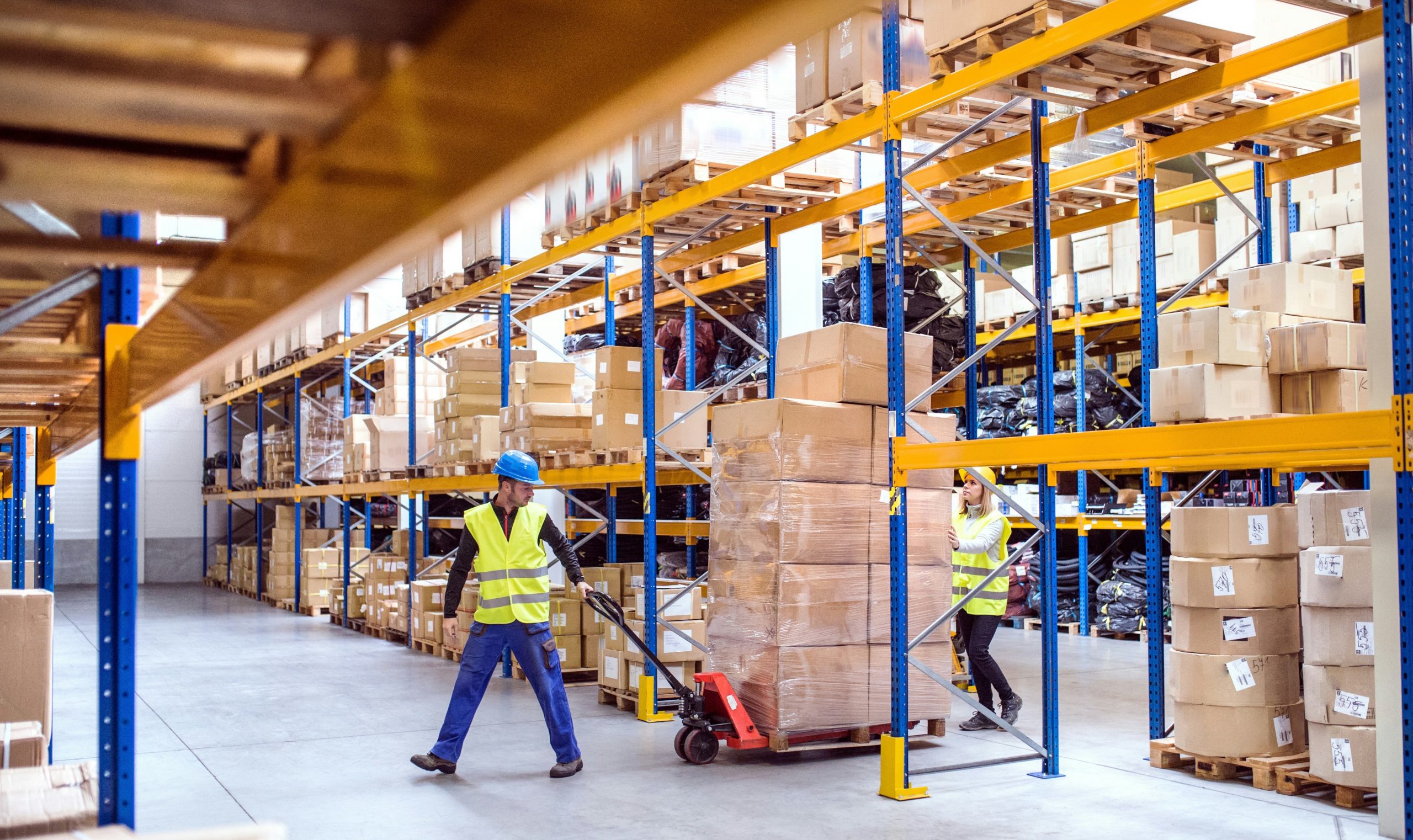
Steps to optimise your warehouse layout
Analyse your existing layout
Start by assessing the current layout to understand which areas require improvement and which approach you’d like to take. Important factors to consider include travel time, storage density, and congestion points. Identifying which items are most frequently accessed and if they’re positioned in easily accessible locations means you can work to improve certain areas and decide which parts of the business need the main focus.
Map out the Workflow
Develop a workflow map to understand how goods move through the warehouse. Ideally, goods should flow from receiving to storage, picking, packing, and finally dispatch, with minimal backtracking or crossing paths. This reduces delays and improves safety, however, without an effective warehouse layout, this process can easily become disorganised, leading to wasted time and potential errors.
Key elements to consider in the workflow:
- Receiving and unloading
- Storage zones
- Picking and packing areas
- Quality control zones
- Dispatch and shipping areas
Implement zoning based on product demand
Using demand-based zoning to position high-demand items closer to picking and packing areas means that travel time is minimised for pickers and speeds up order fulfilment. Here are the three main zones used throughout warehousing”
- Fast-Moving Zone: Place high-demand items closest to picking stations
- Medium-Moving Zone: Keep items with moderate demand slightly further away
- Slow-Moving Zone: Position low-demand items at the back or on higher shelves
Maximising space with vertical storage solutions
If floor space is limited in your warehouse, consider vertical storage solutions such as mezzanine floors or high-rise shelving in order to make use of the surrounding areas. These methods allow you to store more inventory without increasing the footprint of your warehouse, resulting in greater space efficiency and even more room for other utilities such as offices.
Design effective aisles and racking systems
The arrangement of aisles and racks significantly impacts warehouse efficiency, especially when it comes to picking and packing. Every business is different in terms of inventory so ensure to select racking systems that best suit your product type, such as pallet racks for bulk goods or shelving for smaller items.
Leverage technology
Modern warehouse management systems (WMS) and automation tools can provide valuable data to guide layout decisions. For example, a WMS can track inventory turnover, highlight high-demand products, and optimise storage locations. There are also other systems including: barcode scanners and labelling systems to improve tracking accuracy, automated guided vehicles (AGVs) to transport goods and inventory management software to streamline operations and manage stock levels.
Safety Zones and signage
Considered one of the most important parts of a warehouse, ensuring your layout and systems are safe is crucial. When planning a warehouse, it is important to designate spaces such as safety zones for hazardous materials, anti-slip mats, and use signage to direct traffic flow.
Warehouse layout mistakes to avoid
- Overcrowding the warehouse: Resist the temptation to use every inch of space, as this can lead to congestion and make it harder to move items as well as cause possible health and safety concerns.
- Ignoring Data: Utilise data from your WMS or inventory management software to make informed decisions on layout adjustments.
- Neglecting Safety: Prioritise safety in every layout decision to prevent accidents and costly downtime.